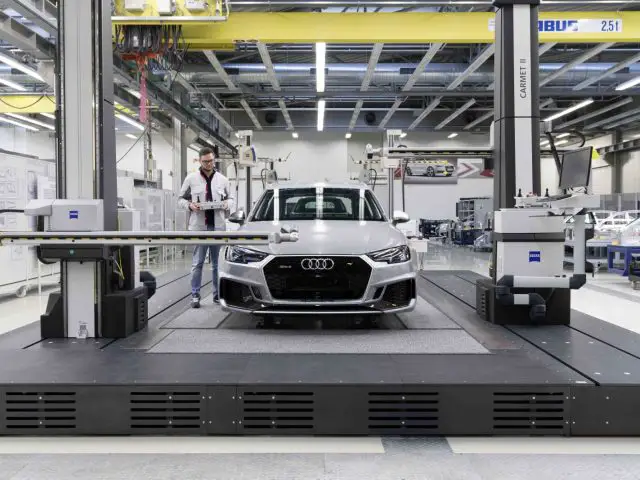
Reportage: indrukwekkende kwaliteitscontrole bij Audi
Dagje meelopen op de afdeling Quality Assurance
![]() |
Door Nile van Leeuwen. Fanatieke autoliefhebber, gedreven autojournalist en ervaren tekstschrijver die zich druk maakt om alles op het gebied van mobiliteit. |
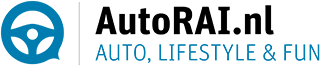
Het succes van Audi is voor een groot deel te danken aan de hoge kwaliteit van de auto’s. Niet alleen op het gebied van de gebruikte materialen. Maar ook de afwerking, de pasvorm van onderdelen, de elektrische systemen, de aandrijftechniek, de onderdrukking van geluiden en trillingen enzovoort. Om de kwaliteit van de Audi-modellen continu te verbeteren, werken er maar liefst 2.800 mensen op de afdeling Quality Assurance. Wij lopen een dag mee in de Audi-fabriek in Ingolstadt, om met eigen ogen te zien hoe ontzettend veel moeite Audi doet om een kwaliteitsproduct te leveren.
Geen foto’s aub
We zijn nauwelijks binnen de poorten van Audi AG – in het zuiden van Duitsland – als de camera’s van onze smartphones en tablets worden afgeplakt. Het is duidelijk dat we dingen te zien krijgen die Audi niet met de buitenwereld wil delen. Logisch, want Audi is op diverse manieren toonaangevend in de auto-industrie.
Innovaties waaraan jaren gewerkt is en waarin ik-weet-niet hoeveel miljoenen geïnvesteerd zijn, wil je niet prijsgeven. Daarbij gaat het niet alleen om prototypes van toekomstige modellen met nieuwe techniek. Ook de technologie die gebruikt wordt bij de kwaliteitscontrole van modellen en afzonderlijke componenten kan uniek, vooruitstrevend en dus zeer waardevol zijn voor een andere autofabrikant.
Dat is ook de achterliggende gedachte van diverse workshops die we deze dag volgen. Audi maakt steeds meer gebruik van digitale processen. Daarmee kunnen kwaliteitstests preciezer en sneller worden uitgevoerd.
Pasvorm van componenten
Een van de belangrijkste vormen van digitalisering bij de kwaliteitscontrole van Audi is bedoeld om de pasvorm van componenten voor het in- en exterieur te controleren. Een model dat volgens de geplande specificaties is gebouwd, wordt door speciale camera’s en optische sensoren gescand. Grote robotarmen dansen om de auto heen en meten de grootte en de regelmaat van naden tussen de verschillende (plaat)delen en oneffenheden in het oppervlak.
Behalve dat hiermee veel nauwkeuriger wordt gemeten, gaat het ook veel sneller. Alle data wordt opgeslagen en op grote beeldschermen wordt haarfijn aangegeven waar eventuele verbeteringen nodig zijn. Zonder de carrosserie aan te raken, worden in enkele uren tot wel miljoenen controles uitgevoerd. Deze kwaliteitscontrole is ook voor het interieur te gebruiken. En ook niet onbelangrijk: deze kwaliteitscontrole kan al 2,5 jaar voor het begin van de serieproductie starten. Met de traditionele methode is dat tien maanden voor de productie.
LEES OOK: Autotest – Audi Q5 2.0 TFSI quattro (2017)
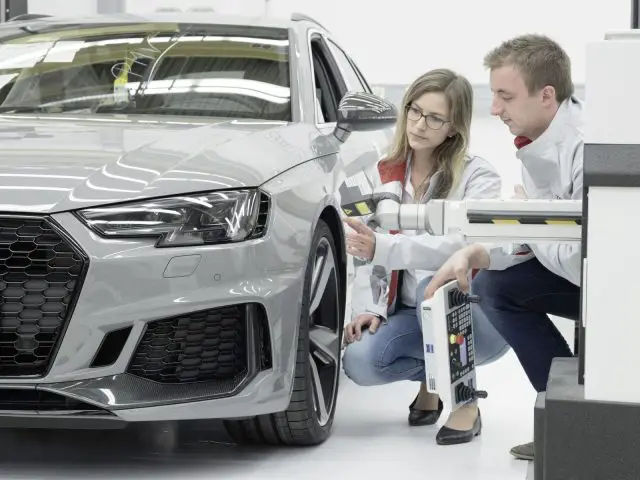
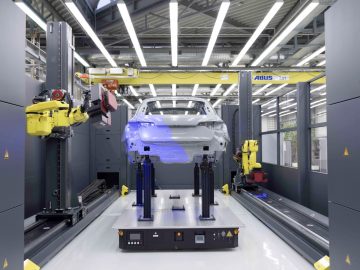
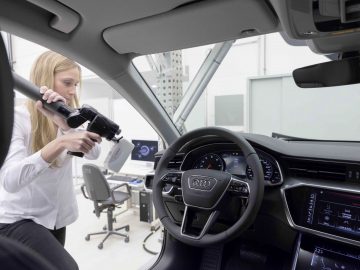
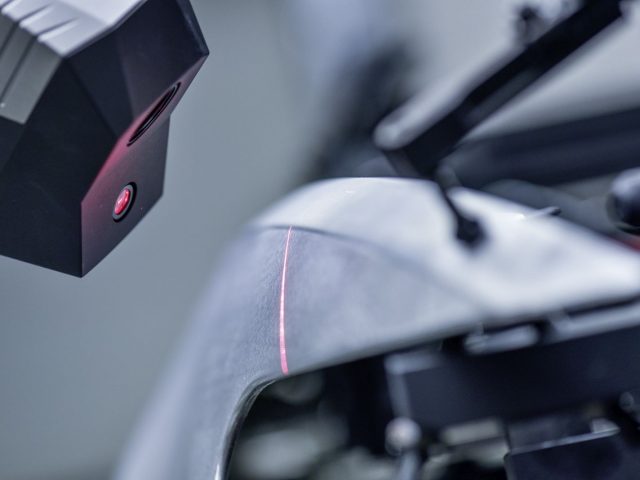
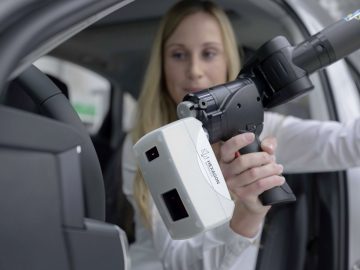
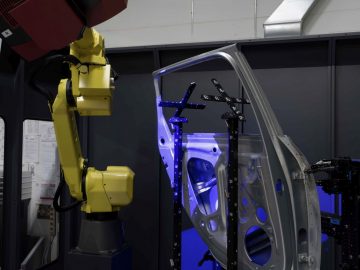
Audi Semiconductor Lab
We gaan naar de volgende afdeling: het Audi Semiconductor Lab. Zoals de naam al doet vermoeden, begeven we ons in een laboratorium. Eentje uit het boekje, met mannen in witte jassen en bureaus vol microscopen en flesjes met chemische goedjes. Hier houden de ingenieurs zich bezig met preventief kwaliteitsmanagement op het gebied van halfgeleiders (semiconductors). Zeer belangrijk, want die maken meer dan 80 procent van alle innovaties in de auto-industrie mogelijk.
Halfgeleiders zijn onmisbaar in elektronische componenten. Het gaat hier om microscopisch kleine materialen en onderdeeltjes waaruit een (micro)chip is opgebouwd. Daarvan zitten er tegenwoordig duizenden in een auto. Je weet wel, die kleine dingetjes die op zo’n groene printplaat zijn gemonteerd. De betrouwbaarheid van een elektronisch systeem is afhankelijk van de betrouwbaarheid van halfgeleiders. Ze dienen niet alleen minimaal vijftien jaar mee te gaan, maar moeten ook feilloos functioneren bij temperaturen van -50 tot +125 graden Celsius.
Recente innovaties waarbij halfgeleiders een belangrijke rol spelen, zijn bijvoorbeeld de OLED-verlichting van de nieuwe Audi A8 en Audi TT RS en de geavanceerde, veelomvattende detectiemodule in de voorbumper van de A8. Audi is het eerste merk dat hiervoor een lasersensor toepast.
Chips zijn ook essentieel bij de ontwikkeling van de zelfrijdende auto. Behalve dat die uiterst betrouwbaar dienen te zijn onder alle omstandigheden, moeten die ook zeer snel informatie doorgeven. De technici op het Audi Semiconductor Lab zijn van mening dat de snelheid van de data-overdracht mede bepaald wordt door de grootte van de halfgeleider. In het laboratorium wordt – in samenwerking met de chipfabrikant – gewerkt aan transistors met een grootte van slechts 10 nanometer!
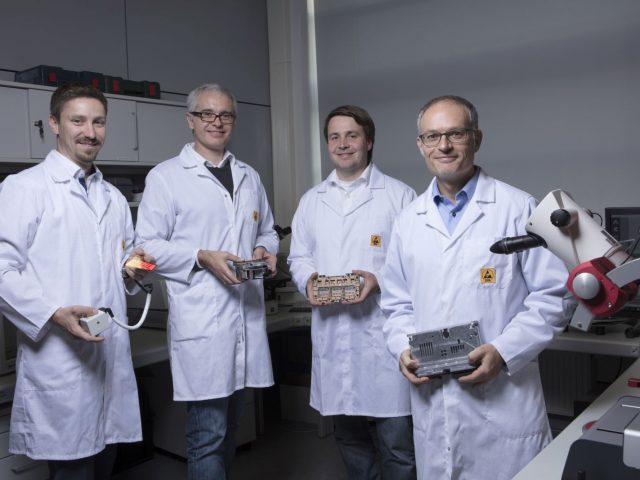
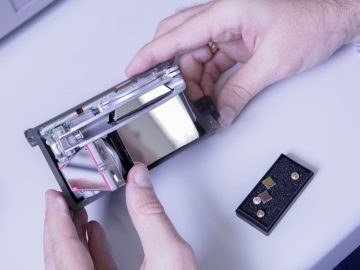
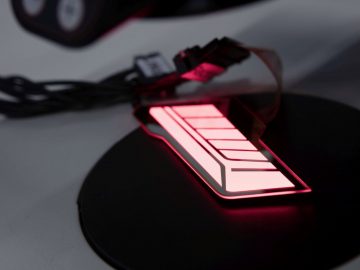
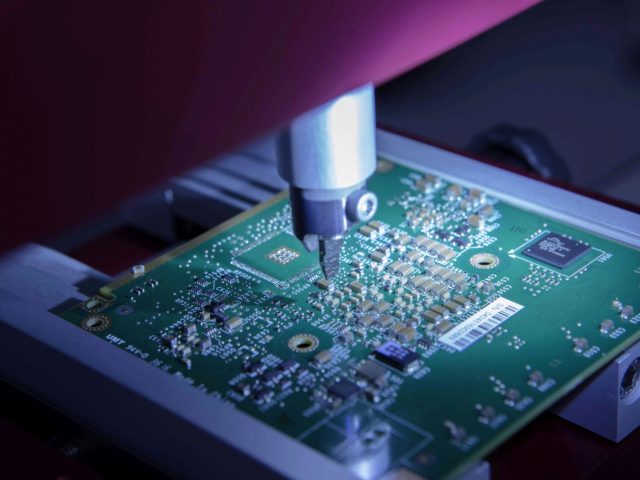
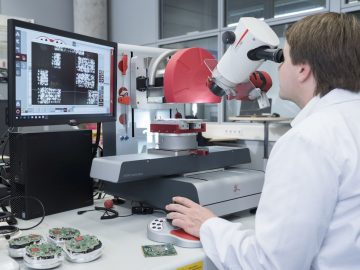
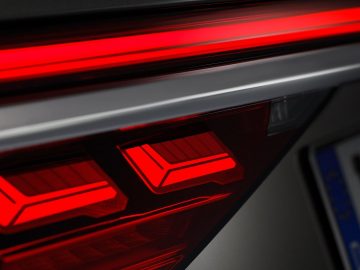
Inzicht in materialen
Maar wat als een (elektrisch) onderdeel defecten vertoont of niet het gewenste resultaat oplevert? Of als materiaal breuken vertoont of (te) snel veroudert? Om de kwaliteit te kunnen blijven waarborgen en verbeteren moet dat dus onderzocht worden. En steeds complexere systemen en materialen vragen om steeds complexere onderzoeksmethoden.
Sinds vier jaar maakt Audi gebruik van FIB (Focussed Ion Beam). Dit is een combinatie van een beeldscannnende elektronenmicroscoop en een ‘ionen-geweer’. Met behulp van een enorm apparaat met zeer, zeer geavanceerde techniek kunnen materialen ‘inwendig’ worden onderzocht. FIB maakt een voor het oog onzichtbaar gat in alle soorten materiaal en scant het laag voor laag, van metaal en glas tot keramiek, polymeer en zelfs leder.
Een mooi voorbeeld dat we te zien krijgen, is een touchscreen waarin een paar vreemde vlekken zitten. Zoiets hadden de technici nog niet eerder gezien. Door het beeldscherm in het apparaat te leggen, wordt letterlijk in het glas van de touchscreen ‘gegraven’. De technici kijken op een beeldscherm mee en kunnen op microscopisch niveau problemen ontdekken en op basis daarvan de kwaliteit verbeteren. Dankzij deze kwaliteitscontrole werd het defect vastgesteld en kon het product in nauwe samenwerking met de fabrikant worden verbeterd. Dit geoptimaliseerde, kraakheldere beeldscherm wordt nu toegepast in de nieuwste Audi A8.
Een andere methode om materialen ‘inwendig’ te analyseren, is Scanning Electron Microscopy (SEM). Hiermee worden röntgenachtige beelden van hoge resolutie gemaakt en op een beeldscherm getoond. Met deze methode wordt de concentratie chemische elementen in een materiaal zichtbaar en kunnen eventuele breukvlakken worden opgespoord. Deze kwaliteitscontrole is van grote waarde bij de productie en continue verbetering van de aardgastanks voor de Audi g-tron modellen.
LEES OOK: Nieuwe A7 Sportback: in de voetsporen van de Audi A8
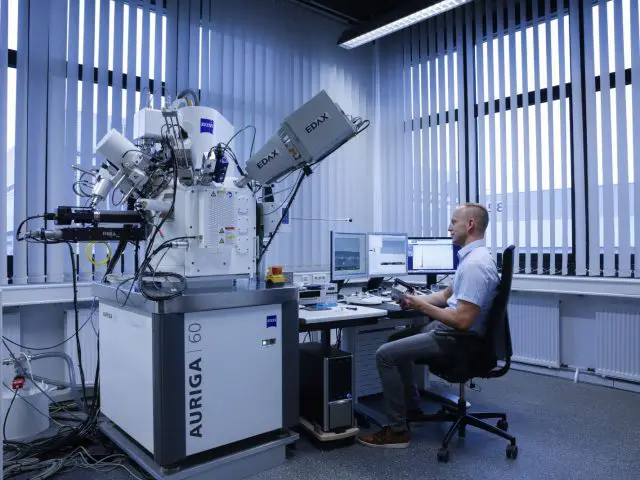
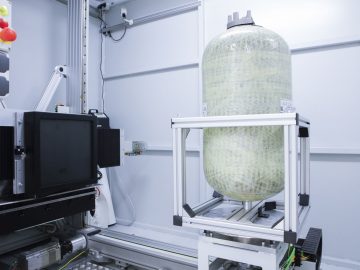
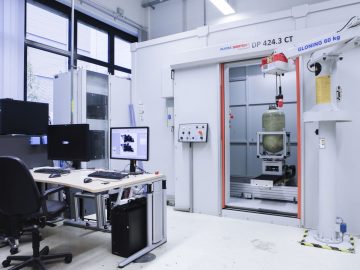
Testen op de weg
Voordat een Audi in productie gaat, wordt die natuurlijk uitgebreid getest op de weg. Deze zogenoemde ‘shakedown-tests’ beginnen een half jaar voor de productiestart. Om een zo hoog mogelijke kwaliteit te kunnen garanderen, is het belangrijk om de auto te testen in de extreemste omstandigheden en zo veel mogelijk gegevens te verzamelen.
Dat gebeurt dan ook, maar veel intensiever dan je zou denken. Bij Audi worden per dag ongeveer zeshonderd auto’s getest, verspreid over de hele wereld, in verschillende omstandigheden en bij temperaturen variërend van -30 tot +50 graden Celsius. De shakedown-tests zijn per jaar samen goed voor zo’n 700.000 draaiuren en 35 miljoen testkilometers. De focus ligt niet alleen op de pure rijeigenschappen, maar ook op het uithoudingsvermogen van componenten en het gebruiksgemak van de (elektronische) voorzieningen.
De testrijders maken gebruik van tablets met checklijsten die zij moeten afwerken. Alle (elektronische) voorzieningen en rijhulpsystemen moeten keer op keer worden getest in verschillende situaties. Alle bevindingen na de controle van een bepaald systeem worden door de testrijder op de tablet ingevoerd voordat het volgende onderdeel getest wordt, zoals een automatisch parkeersysteem, adaptieve cruisecontrol, waarschuwingssensoren en andere veiligheids- en assistentiesystemen.
Tijdens de testritten worden alle gegevens verzameld. Op de achterbank van de auto ligt een enorme server van wel 35 kg. Met modellen als de Audi A4, A5, Q5 en Q7 wordt per werkdag van acht uur 10 GB aan data verzameld. Bij de nieuwe Audi A8 en A7 Sportback zelfs 50 GB! Alle data wordt door een andere afdeling geanalyseerd.
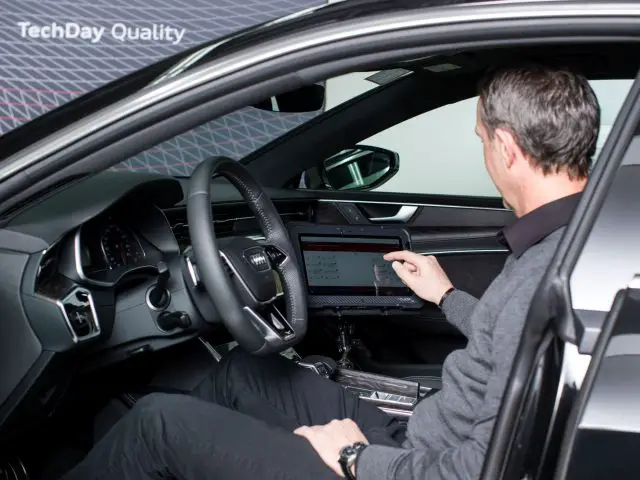
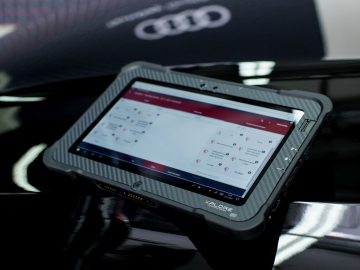
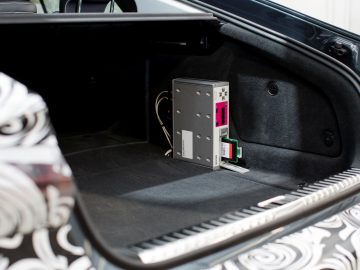
Service Technologie
De kwaliteitscontrole stopt niet als de Audi eenmaal in de showroom staat. Service Technologie is een integraal onderdeel van Audi Quality Assurance en vormt een link tussen Audi AG en de gebruiker.
Service Technologie werkt met wereldwijde Technische Service Centres waar voertuiggegevens worden geanalyseerd. Alle gegevens worden doorgegeven aan Audi, bijvoorbeeld aan de afdelingen ontwikkeling en productie. De speciaal voor Audi ontwikkelde Car Assyst-app speelt daarbij een belangrijke rol. Hiermee is draadloze diagnose van voertuigen mogelijk. Eventuele problemen worden zo direct zichtbaar.
Het is Audi zelfs gelukt om een subjectieve beleving van NVH (Noise, Vibration and Harshnes: rammeltjes, piepjes en kraakjes) te objectiveren en analyseerbaar te maken. Daarvoor wordt een proefrit met de klant gemaakt en worden alle vibratie- en geluidsniveaus opgenomen. Deze gegevens worden vervolgens vergeleken met data van andere voertuigen die om dezelfde reden in de werkplaats kwamen.
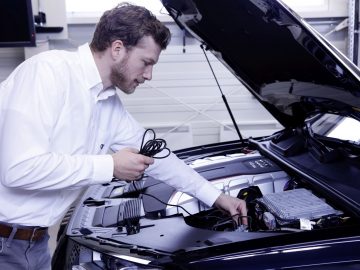
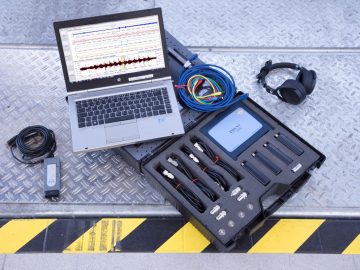
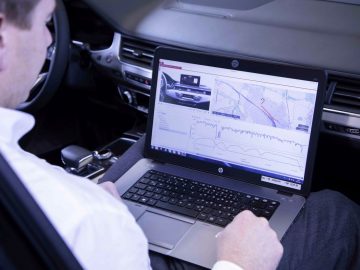
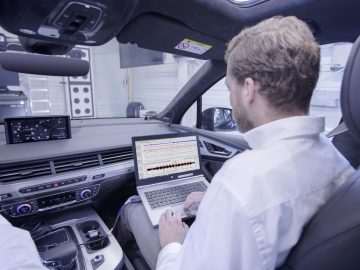
Na een hele dag te hebben meegelopen en diverse afdelingen te hebben gezien, is duidelijk dat de kwaliteitscontrole bij Audi véél verder gaat dan verwacht. De omvang van de afdeling Quality Assurance is immens. De apparatuur die wordt gebruikt, is van een andere wereld. Als je ziet hoe schoon sommige afdelingen zijn en hoeveel academici er rondlopen, lijkt het soms net een ziekenhuis.
Maar het resultaat mag er zijn. Of je een Audi wel of niet mooi vindt, en of het rijgedrag je wel of niet aanspreekt; elke Audi maakt indruk op het gebied van kwaliteit, afwerking en materiaalgebruik. Daarover is iedereen het eens. En nu weten we waarom.
LEES OOK: Audi werkt aan kunstmatig intelligente auto